The Practical Playbook for Agile Manufacturing Executives
Introduction
Are errors eating into your capacity and profits? This question resonates with manufacturing leaders across North America who are grappling with an increasingly challenging production environment. Over the past two decades, we have had the unique opportunity to work with hundreds of factories producing high-tech products in industries ranging from defense, aerospace and medical devices to industrial electronics, heavy machines and precision laboratory instruments. A consistent theme has emerged: factory managers and executives are struggling to eliminate human errors in their manufacturing processes, while training has become a significant burden on their organizations.
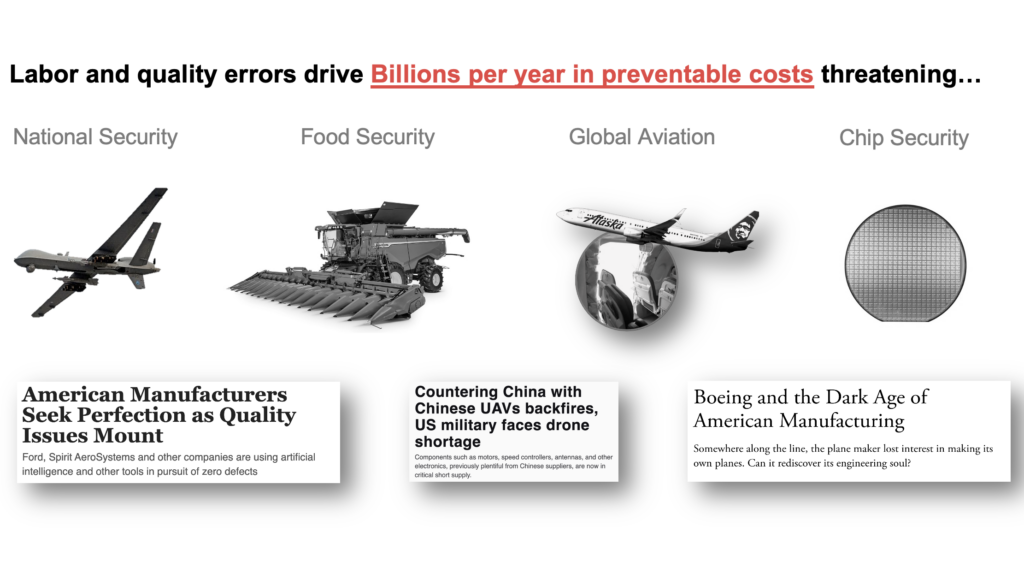
Current Manufacturing Crisis
Labor and Training Challenges
Executives report the manufacturing workforce landscape has transformed dramatically. Training time for new workers has doubled over the past 20 years: What once took 3-6 months now requires 6-12 months. More critically, we hear that mechanical hand skills and technical aptitude of new manufacturing workers have declined substantially. Where factories report they once could easily hire skilled millwrights, they now find themselves training people who lack the fundamental technical knowledge factories need.
Within the most advanced manufacturing organizations, interviewing five line workers how they complete a complex manual assembly process more often than not results in five different answers. This highlights a critical gap with experienced operators who may have developed their own version of the assembly process, but this knowledge is not well shared or known within the organization. The differences in technique or step sequences result in significant differences in overall assembly cycle time, quality of workmanship and ultimately means the company does not own the process knowledge, it’s only known by its experienced workers.
This knowledge and skills gap creates a cascade effect, as training responsibilities fall to supervisors and senior assembly workers, impacting overall productivity. Meanwhile, manufacturers report they compete for labor with gig-economy platforms offering flexible working arrangements, further complicating recruitment and retention.
Quality Control Crisis
Quality challenges extend beyond workforce issues with manufacturing executives reporting:
- Manufacturing has become increasingly complex, with high-tech electronics, wiring and sensors embedded in more products than ever before.
- Executives report 20% to 50% of their products may require rework due to avoidable human assembly mistakes.
- Common errors include component substitution, swapped wires and cables, incorrect labels and serial numbers, improperly installed parts, and missing components just to name a few.
- Design for Manufacturing (DFM) issues continue to compound these challenges by negatively impacting yield and manufacturing labor requirements.
End Customer Impact
When quality issues reach end customers, the damage extends far beyond immediate costs. The credibility hit of customers asking “how did you miss something so simple” is just the beginning. Our research reveals the true scope of warranty and customer satisfaction costs that include:
- Manufacturers report they ship entire replacement products to job sites, incurring thousands of dollars in costs per warranty claim.
- Companies maintain dedicated service teams that travel with spare replacement parts, knowing products are shipping with missing components they add during installation.
- In multiple facilities, we have observed chained-off areas containing millions of dollars in returned stock: Entire shipments rejected by corporate customers who found just a couple of defective products in the batch.
- When critical safety systems are compromised by human error, such as airplane door bolts, the costs multiply exponentially to include lawsuits or settlements.
- The costs due to quality issues can easily exceed 10% of annual factory revenue when accounting for the myriad of challenges facing modern manufacturers.
The Hidden Capacity Thief
Critically, the example quality and training challenges are silently stealing factory capacity. With 20% to 50% of products requiring rework, facilities are losing a corresponding percentage of their potential throughput. In cases involving adhesives, epoxies, or other permanent bonding agents, simple assembly mistakes can result in complete product write off as rework is not economically viable. This pattern repeats across industries and regions, affecting any manufacturer producing complex, modern products.
Reclaiming Factory Capacity and Profits
The good news is that manufacturing leadership teams can take immediate, actionable steps to get their facilities back on track and win back lost profits and capacity. We use the following comprehensive approach to take a holistic perspective to the manufacturing process.
Root Cause Analysis
Understanding the source of errors is paramount and executives must determine whether issues are:
- Design related, where simple changes can make a significant improvement to yield and error rate.
- Process related, requiring additional controls or procedure changes.
- Vendor related, with sub suppliers failing to deliver consistency and quality according to expectations.
- Training related where additional guidance could instill best practices for new and experienced manufacturing workers.
- A combination of all which manufactures regularly report, requiring a balanced approach.
Design-Related Issues
Manufacturing challenges often stem from design issues, but solutions must be practical and encompass:
- Regulatory or compliance requirements.
- Cost and ROI considerations may limit design modification options.
- Production controls that could be implemented where design changes aren’t feasible.
- Unique product or design requirements that require case-by-case assessment.
- Where design-related issues are present, a holistic look at the New Product Introduction process may be beneficial and covered in another white paper.
Process Related Issues
Human-introduced mistakes often stem from systemic issues including:
- Missing or incomplete work instructions or procedural documentation.
- Lack of available training and oversight by experienced supervisors.
- Technical engineering drawings that are difficult for laypeople to interpret.
- Complex or intricate process steps that are difficult to reproduce.
- Enviromental conditions including temperature, humidity and PPE controls
- Design related issues that trigger additional steps by the human operator to compensate.
Vendor Related Issues
Vendors over time can become complacent in the delivering of high-quality products to your organization. When making an assessment we start by looking at the following issues:
- Does your organization have well documented specifications and standards for the vendor and part in question.
- Assessing whether the vendor deviations are within your design spec or whether the specifications lack required controls to meet your actual production quality needs.
- Incoming QC checks on vendor supplied parts to ensure they meet the specification requirements add cost and time to incoming material.
- On the line QC checks on vendor supplied parts lead to additional load and work on the assembly workers in your organization.
- Does the vendor have sufficient controls in place within their organization to meet your quality and consistency requirements.
Training Related Issues
Training is an ongoing challenge for nearly every manufacturer we speak with and some of the following questions may unearth some critical truths that help in your quest:
- Does your organization have well documented procedures or work instructions for every manufacturing process.
- When new employees start, are they able to learn everything they need by reading the documented work instructions or do they rely heavily on other staff members to teach tribal knowledge.
- Who within your organization oversees training existing manufacturing workers to ensure continuous upskilling and compliance with documented procedures.
- Are the manufacturing steps repeatable, scalable and teachable in written format. If they are not, it is worth investigating other mediums such as video that transcend language and literacy barriers.
Quality System Compliance
All planned changes and solutions must align with enterprise quality management systems such as ISO 9001 or Industry-specific systems like such as IATF 16949 or AS9100. Any implemented solution must contain a method to track changes to ensure ongoing compliance and auditability within your quality management system.
Change Management in Live Production
Making changes to live production presents unique challenges but can be successfully managed through:
- Strategic planning with experienced staff members and implementation partners.
- Empowering people within your organization to contribute to shaping the direction and process.
- Preparation of personnel for any planned operational changes.
- Designation of internal champions to guide and own the change process.
- Continuous and objective measurement and iterative adjustment of implementation strategies enables an agile, continuous learning environment.
Impact Measurement and Prioritization
The most successful transformation programs optimize resource allocation by:
- Objectively measuring the impact of each identified issue.
- Focus their team’s attention on the most critical problems.
- Remove human bias from problem prioritization by developing measurable KPIs.
- Determine issue criticality based on available data to gain a high confidence solving the issue will deliver real, tangible results for their organization.
Taking the Next Step: Technology-Enabled Solutions
After quantifying root cause and measuring impacts, you are well positioned to identify the right solution or partner for your organization. New to industry, AI-powered manufacturing co-pilots have already demonstrated remarkable proven results with:
- Continuous real time AI Co-pilots that automate monitoring of the manual manufacturing process steps to eliminate errors by line workers.
- Automated visual inspection of products by AI Co-Pilots that offload valuable human workers from monotonous and repetitive tasks.
- Automated training of manufacturing workers with video instructions that transcend language and literacy and are understandable by the layman.
- Objective metrics tracking every product manufactured including a comprehensive quality score, step by step cycle time, defects detected and bottlenecks in overall factory performance.
- Controls for managing all changes to the process including automated version and release management to ensure compliance with your quality management system.
- Capture and retention of photographic and video data of every manufacturing step to build a database of your process knowledge you can leverage to supercharge overall design and manufacturing improvements.
For more information about implementing solutions in your organization, contact Rapta, your transformational partner, to help you work through the next steps of your journey. We help manufacturers across the US achieve:
- 20% – 30% increase in revenue capacity through enhanced throughput.
- 90% reduction in error-related costs, saving millions annually.
- 10x faster video-based training that is as easy to understand as YouTube.
- Capture and Ownership of your production knowledge.
- Powerful analytics and reporting to optimize process and deepen understanding.
- Return on investment within months.
About the Author
Aaron is the CEO and Co-Founder of Rapta, Inc. Prior to Rapta, Aaron led the first innovation team at Stanley Black and Decker to commercialize an applied AI product to drive increased productivity in jobsites. In a career spanning 22 years working at the intersection of Software, AI and industrial manufacturing, Aaron has deployed operational solutions for Fortune 500 businesses and SMEs. Aaron is passionate about building products that give our customers an unfair advantage in manufacturing and ensuring we own our future through sovereign manufacturing. Read more.