Electronic Assemblies: Board Insertion and Final Assembly
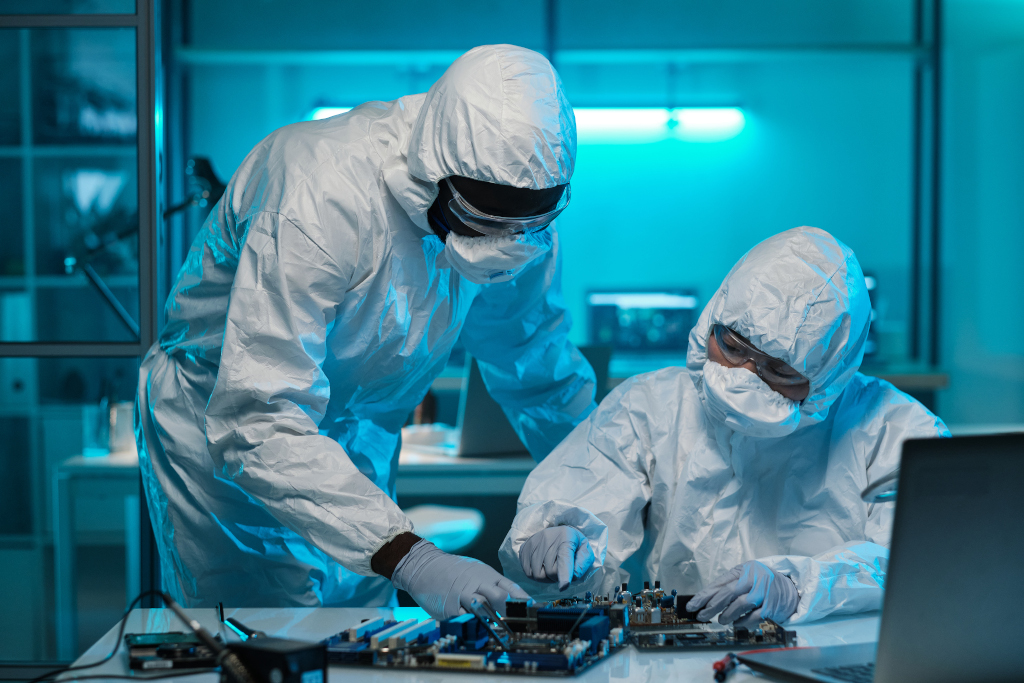
The majority of electronic assemblies require a series of manual steps to deliver a complete finished product to the end customer. These assembly steps may include:
- Installing the PCB assembly into a housing
- Placing a heatsink pad on heat generating components
- Installing a wiring harness and making one or multiple connections
- Screwing, clipping or ultrasonic welding the housing in place
- Potting, encapsulation, glueing or coating
- Applying stickers, barcodes or other marking and branding
It’s critical each of these steps are completed exactly according your standard work instructions. Failure to perform these steps correctly can lead to product recalls, significant costs and damaged reputation. Rapta ensures each and every one of the products you ship are complete according to your standard work instructions and we provide full video traceability for every assembly we validate.
In this video you will see Rapta’s AI Supercoach guiding the assembly worker, in real time through the correct assembly steps and providing real time quality assurance by identifying defects and correct remediation. Rapta’s touchscreen interface provides the operator with real time visual and audible feedback when a defect occurs so they can fix immediately. All work instructions are video based so they are easy to understand, follow and learn quickly.
Electronic Assemblies: Masking for Conformal Coating
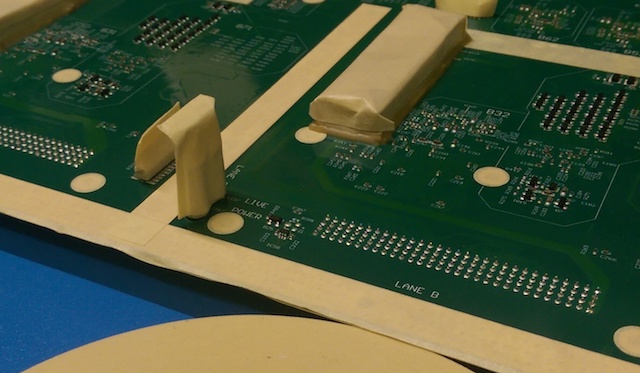
Conformal coating offers PCB assemblies protection against harsh environments including water, condensation, humidity, chemicals or other elements that may adversely impact their intended operation. Some PCB assemblies may be conformally coated with an automated process however for many designs this is not feasible due to size, spacing or sensitivity of components to indirect spray. For these PCB assemblies manual taping of connectors and other components is required which is time consuming and if done incorrectly can result in yield loss and impacts to the bottom line.
In this video you will see Rapta’s AI Supercoach guiding the assembly worker, in real time through the correct masking steps and providing real time quality assurance by identifying defects and correct remediation. Rapta’s touchscreen interface provides the operator with real time visual and audible feedback when a defect occurs so they can fix immediately. All work instructions are video based so they are easy to understand, follow and learn quickly.
Industrial Control Panel: Component Wiring
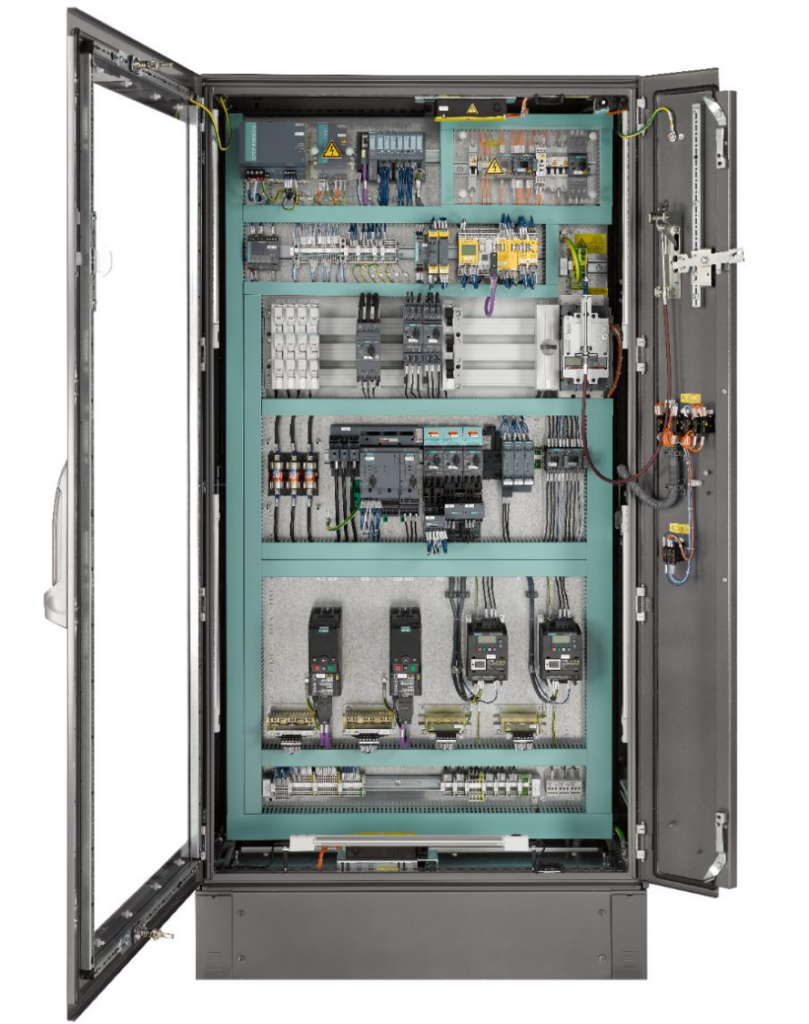
Industrial control panels are a critical piece of infrastructure within your manufacturing environment and are often assembled by specialist businesses. Incorrect wiring and loose connections are a major safety and fire risk and can lead to significant damage to the panel, connected capital equipment or building. These assemblies are manually constructed and subject to the skill of the line worker making copy exact a challenge in a production environment.
In this video you will see Rapta’s AI Supercoach guiding the line worker, in real time to make the correct component wiring connections. Rapta works in real time and helps you deliver copy exact by providing AI quality assurance that identifies incorrect wiring and deviations outside of the standard work instruction. Rapta’s touchscreen interface provides the operator with real time visual and audible feedback when a defect occurs so they can fix immediately. All work instructions are video based so they are easy to understand, follow and learn quickly.
Electronic Assemblies: Manual Soldering
Many electronic assemblies require manual hand soldering due to production volume, board complexity or proximity to other components preventing wave or selective soldering. Continuously meeting J-STD-001 from the IPC is subject to the skill of the human operator in a continuous production environment. Rapta offers a real time, inline solution that inspects the quality of key solder joints during manual soldering. We can detect a variety of issues depending upon your application including:
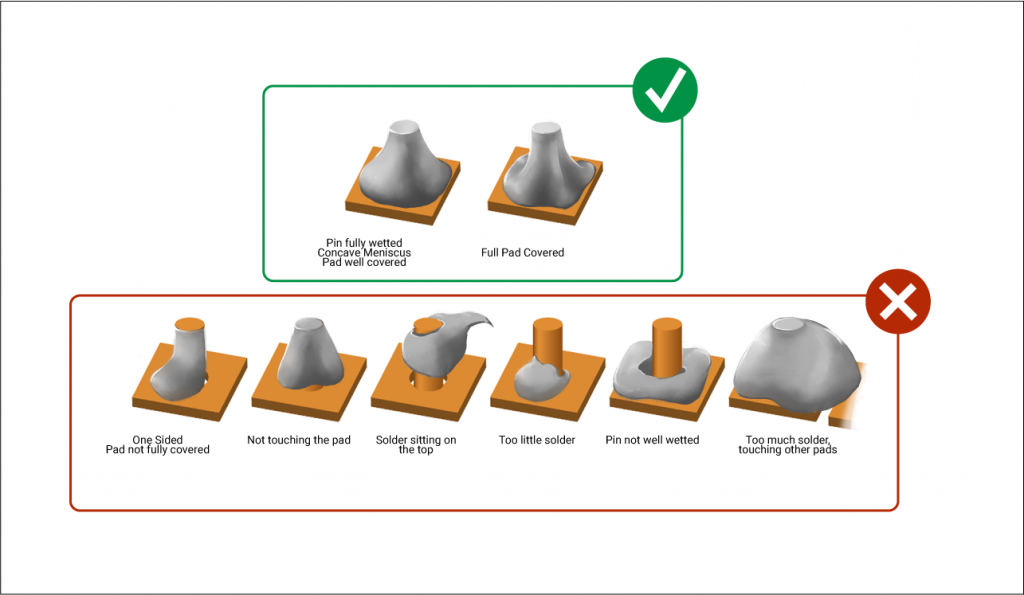
In this video you will see Rapta’s AI Supercoach guiding manual soldering in real time and identifying defects. Rapta’s touchscreen interface provides the operator with real time visual and audible feedback when a defect occurs so they can fix immediately. All work instructions are video based so they are easy to understand, follow and learn quickly.
Mechanical Assembly
Mechanical assembly is cornerstone to a multitude of industrial manufacturing processes in automotive, aerospace, heavy industrial and other applications. Manual assembly processes are subject to operator experience and it’s critical each of these steps are completed according to your standard work instructions. Failure to perform these steps correctly can lead to product recalls, significant costs and damaged reputation. Rapta ensures each and every product you ship are completed according to your standard work instructions.
In this video you will see Rapta’s AI Supercoach guiding the assembly worker, in real time through the assembly steps and providing real time quality assurance by identifying defects and correct remediation. Rapta’s touchscreen interface provides the operator with real time visual and audible feedback when a defect occurs so they can fix immediately. All work instructions are video based so they are easy to understand, follow and learn quickly.
Preventing product recalls due to assembly issues
We recently got a product recall notification for our DeWalt compound miter saw, a really great saw that we use regularly. The unfortunate part is this should have never happened and as a result there are 1.4 million miter saws recalled with a cost that might number in the tens of millions. Rapta prevents this from happening by catching quality issues as they happen on the factory floor and holds shipping of products that are not certified. We can determine if the manufacturing process meets the expected quality level and in real time pick up small deviations from the standard work instruction. Want to make sure your brand never has to live through recalling millions of products?
In this video you will see Rapta’s AI Supercoach guiding the service worker, in real time through the repair steps and providing real time quality assurance by identifying when things like brackets are not aligned. Rapta’s touchscreen interface provides the operator with real time visual and audible feedback when a defect occurs so they can fix immediately. All work instructions are video based so they are easy to understand, follow and learn quickly.
Have a unique requirement or manufacturing challenge? Reach out to our team of specialists to find out how we can help your business.