In today’s precision manufacturing landscape, ensuring proper torque application isn’t just about quality—it’s about safety, reliability, and preventing costly recalls. Rapta AI’s TorqueGuardian system represents a revolutionary approach to fastener management by combining advanced AI vision systems with sophisticated torque intelligence to overcome one of the most challenging aspects of assembly: prevailing torque management.
Understanding Prevailing Torque: The Manufacturing Challenge
Prevailing torque, also known as running torque, is the driving torque needed to overcome friction in a threaded fastener. This friction-generated resistance occurs before any actual clamping force is applied to join components together.
It may be required to overcome intentional interference designed into bolted joints (like Nylok patches or Tri-Lobe fasteners) or unintentional interference from component variation and quality issues (such as weld spatter, cross-threading, or misaligned holes).
The challenge is significant because:
- Without reliable compensation strategies, prevailing torque can stop the tightening process prematurely or cause operators to move to the next tightening sequence too early.
- In some applications, particularly aerospace, specifications often require a specific torque value “above running torque,” meaning the final torque must dynamically adjust based on the prevailing torque encountered.
- In certain cases, the prevailing torque may actually exceed the joint’s seating torque or even the target torque of the fastening process.
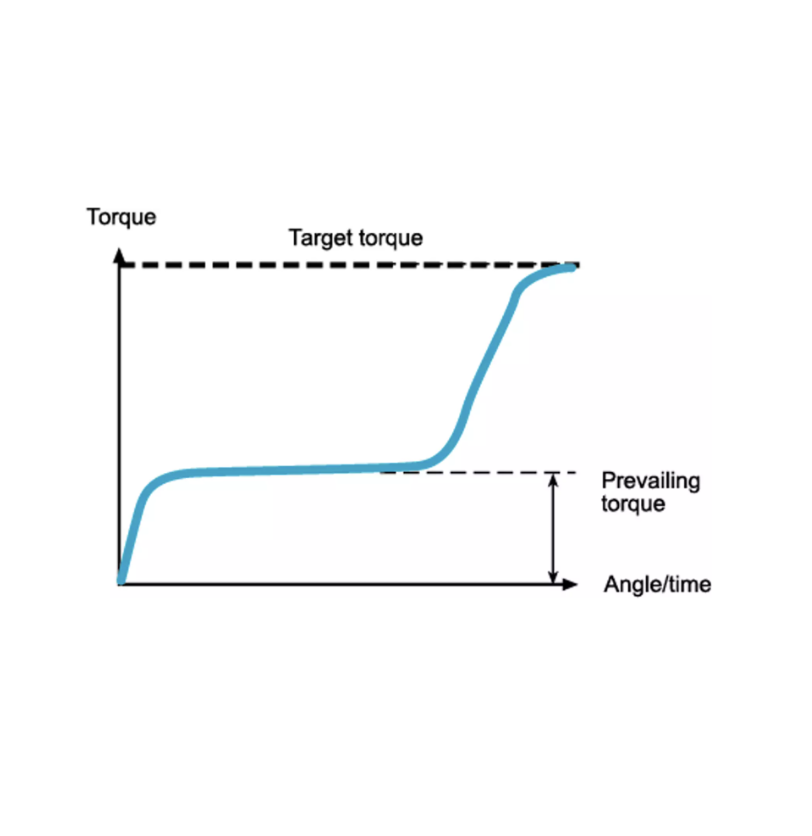
How Rapta AI’s TorqueGuardian Addresses This Challenge
Rapta’s TorqueGuardian takes a comprehensive approach to fastener management, leveraging both visual AI verification and digital torque intelligence:
1. Integrated Digital Torque Sensing
Rapta’s AI platform supports connected torque wrenches that are wired, wireless, or electric drive. This integration allows real-time monitoring of torque application throughout the fastening process, providing data essential for prevailing torque management.
The platform has been tested with various professional equipment including:
- Kolver: KDS-MT1.5 SCREWDRIVER and KDU-1A ADVANCED UNIT
- Ingersoll Rand: QX torque tool and INSIGHTqcx™ Cordless Controller
- Tonichi torque wrenches
2. Visual AI Verification
What truly sets Rapta’s approach apart is its dual-verification system:
The torque verification AI validates that the tool is on the correct part of the assembly and has achieved the correct torque. The AI also validates that after the torque event the fastener is in the correct final spot.
This addresses a critical issue in manufacturing: ensuring not just that proper torque was applied, but that it was applied to the correct fastener in the correct sequence.
3. Prevailing Torque Compensation
By analyzing the torque patterns during fastening, TorqueGuardian can:
Measure the amount of running torque encountered during rundown and dynamically compensate for it by adding it to the total torque applied to the joint. This ensures consistent clamping force across assemblies despite variations in prevailing torque.
4. Real-Time Quality Assurance
In addition to visual inspection of the bolt torquing process, the Rapta platform processes inputs from torque tools to validate that the right event happened to the right bolt with the right amount of torque applied.
This prevents common assembly issues where:
- Problems arise if bolts aren’t torqued in the proper sequence, resulting in components coming loose or compressed gaskets.
- Incorrect torque application goes undetected until product failure
- Fastener installation errors remain hidden until costly testing or field failures
Business Benefits of TorqueGuardian’s Approach
The implementation of Rapta’s TorqueGuardian technology delivers significant business value:
1. Quality Improvement
By eliminating errors and automating QA, Rapta’s AI Manufacturing Co-Pilot increases factory capacity by over 30%. The system catches quality issues in real-time, preventing manufacturing defects from propagating through the production process or reaching customers.
2. Training Enhancement
Novice workers can successfully complete precision assembly tasks after watching the video work instructions for the first time—a process that previously took hours with the most skilled people. This rapid skill transfer is particularly valuable in today’s manufacturing environment facing skilled worker shortages.
3. Recall Prevention
Rapta prevents costly product recalls by catching quality issues as they happen on the factory floor and holding shipping of products that aren’t certified. Given that product recalls can cost manufacturers millions of dollars, this preventative capability provides substantial financial protection.
4. Standardization and Portability
The AI Platform standardizes work instruction across organizations, making it easy to replicate assembly know-how at other manufacturing sites, as well as flex workers across different production lines to fulfill surges or back orders.
Implementation Process
Implementing TorqueGuardian follows Rapta’s streamlined approach:
- Through an intuitive visual setup tool, the platform learns proprietary assembly techniques from just a few correct and incorrect examples.
- The AI automatically generates the training set in just minutes, including augmentations to accommodate varying lighting, color, and physical geometry—contrasting with traditional vision systems, which take weeks to months to train and require thousands of manually captured images.
- Teaching the system an assembly process is done using Rapta’s visual setup tool, where a knowledgeable worker performs the assembly for the system’s cameras. The deep learning AI analyzes the recorded video to learn the correct sequence of steps based on what it was shown, with no coding required.
- Once deployed, the AI Platform delivers continuous training and quality assurance in real-time, ensuring work is completed correctly.
Conclusion: The Future of Fastener Management
Rapta’s TorqueGuardian represents a significant advancement in manufacturing quality control by addressing the complex challenge of prevailing torque. By combining digital torque intelligence with AI vision systems, it ensures that every fastener is torqued correctly, in the right sequence, and with the proper compensation for prevailing torque.
As manufacturing continues to face challenges with skilled worker availability and increasing quality demands, systems like TorqueGuardian demonstrate how intelligent automation can simultaneously improve quality, enhance worker capabilities, and protect companies from costly errors—all while maintaining the flexibility needed in today’s dynamic production environments.
For manufacturers looking to eliminate fastener-related quality issues while improving productivity, Rapta’s TorqueGuardian provides a comprehensive solution that addresses both the technical challenges of prevailing torque and the practical realities of modern manufacturing.
To learn more about how Rapta can solve your critical fastener applications visit our TorqueGuardianTM page.