Rapta, the leader in AI-powered visual quality assurance for advanced manufacturing, announced today that its platform enabled a leading U.S. Department of Defense (DoD) contractor to achieve Full Rate Production (FRP) approval on a mission-critical defense program. The approval marks a significant milestone for the OEM and validates Rapta’s ability to solve one of the most pressing challenges in defense manufacturing: on-time delivery under accelerated New Product Introduction (NPI) schedules.
Faced with high risk of missing Full Rate Production milestones, the defense contractor was under pressure to demonstrate quality control, delivery readiness, and digital traceability. Rapta was deployed as a factory modernization solution to provide real-time QA visibility, active operator video guidance, automated error alerts, and accelerated root cause analysis across complex build stations.
“There was high risk to meeting the Full Rate Production timeline until Rapta was deployed,” said the Engineering Program Lead at the OEM. “The DoD customer explicitly appreciated how quickly we could show traceable inspection results, QA trends, and corrective actions. Rapta played a key role in securing FRP approval.”
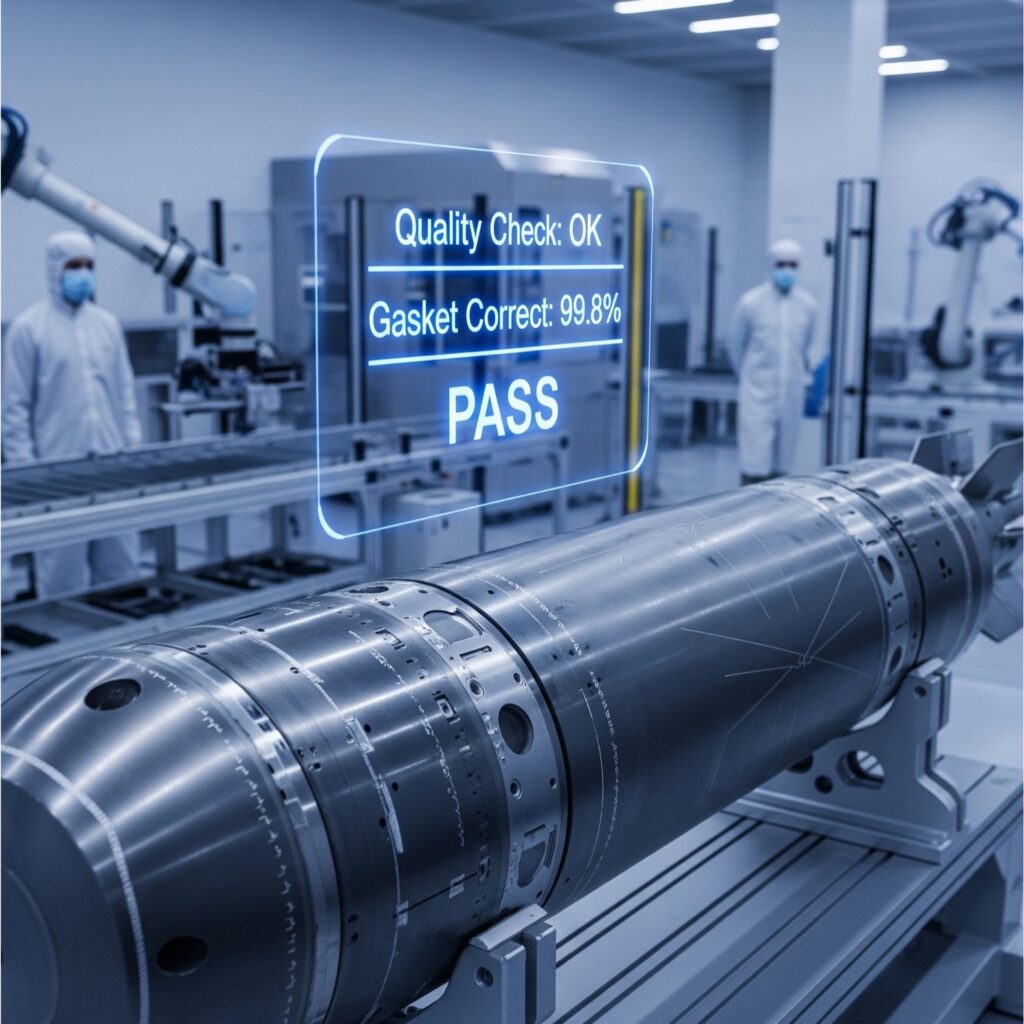
Five Critical Success Factors for Defense Manufacturing at Scale
This customer’s successful path to Full Rate Production approval demonstrates a proven playbook that defense manufacturers can apply when scaling mission-critical programs. Here are the five essential elements that enabled their success:
1️⃣ Quality Automation Ensures Mission Success
Manual quality processes create bottlenecks and drive up costs when scaling production. Automated quality validation catches defects in real-time, ensuring mission-critical standards while maintaining cost efficiency throughout the production lifecycle.
2️⃣ Workforce Readiness at Scale
You can’t hire experienced defense workers overnight. The key is implementing systems that enable rapid training while maintaining the precision standards that experienced workers deliver, ensuring consistent quality regardless of workforce changes.
3️⃣ Complete Production Traceability
Every component, every process step, every decision must be documented and auditable. This isn’t just for compliance – it’s the foundation for continuous improvement, organizational learning, and rapid issue resolution when challenges arise.
4️⃣ Flexible Production Capacity
Defense demand can surge unexpectedly, so successful manufacturers build systems that can scale up or down without rebuilding entire production lines or compromising established processes and quality standards.
5️⃣ Supply Chain Resilience
Defense manufacturing requires secure, reliable supply chains with complete visibility into every component and the ability to quickly validate alternative suppliers when disruptions occur.
By implementing these five pillars alongside Rapta’s AI-powered quality assurance platform, defense contractors can significantly reduce the risk of program delays while maintaining the exacting standards required for mission-critical applications.