TorqueGuardian™: Torque Intelligence for every Fastener
50% FASTER PRODUCTION
ELIMINATE FASTENING DEFECTS
SCALABLE FOR ANY FASTENER
TorqueGuardian™ delivers exceptional return on investment by eliminating manual quality verification processes that traditionally consume valuable production time and resources. By automating both quality checks and tool configuration adjustments in real-time, manufacturers experience immediate cost savings through reduced inspection labor, faster production cycles, and significant reductions in rework and warranty claims. Verifying a fastener has achieved the required number of turns ensures fastening integrity by detecting cross threading, thread debris and under-torque or over-torque failures. This verification includes knowing when operators have used fasteners that are too long or too short for each step. This capability transforms quality assurance by:
- Automatically flagging potential failure points before product completion.
- Creating auditable records of assembly integrity for liability protection.
- Reducing warranty claims through early detection of fastening issues.
- Enabling real-time training opportunities for assembly personnel.
Rapid ROI and Actionable Insights
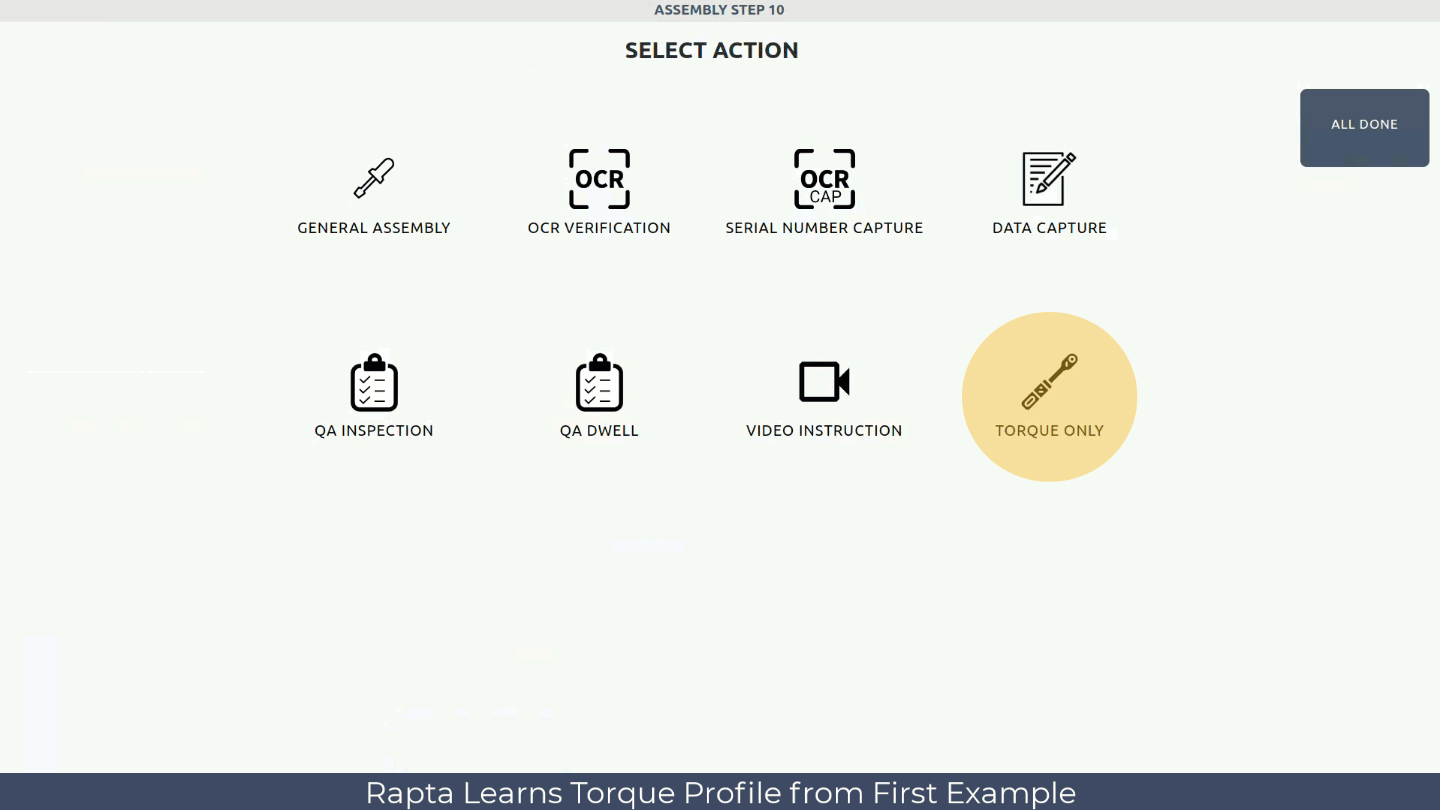
Dynamic Controls for Critical Applications
Once programmed, each fastener can have a unique torque profile including target and min/max torque as well as run-down velocity, giving you exceptional flexibility and precision in your fastening operations. These adaptive controls are perfect for:
- Defense equipment requiring different torque specifications based on environmental conditions.
- Semiconductor manufacturing where precise assembly affects performance.
- Industrial equipment where variable torque requirements exist within a single assembly.
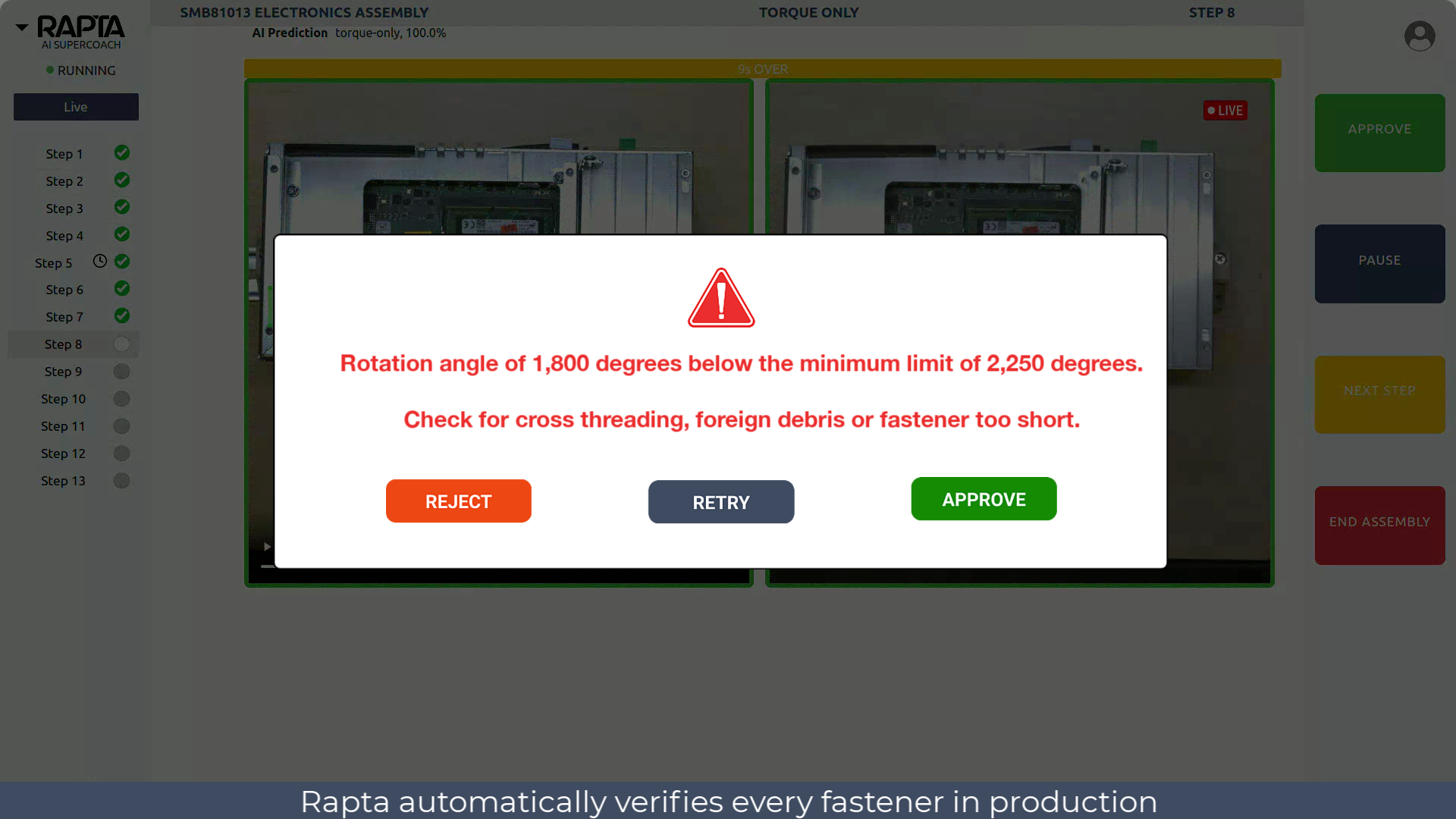
Digital Tracking and Regulatory Compliance
Gain unparalleled insights into design reliability with real time tracking based on actual production data and create a real live digital twin for every production step, keeping your design synchronized with what you are actually producing. The digital twin functionality streamlines compliance through:
- Automated report generation for government safety inspections.
- Data aggregation for ISO certification documentation.
- Simplified auditing processes for regulated manufacturing.
- Evidence-based documentation for continuous improvement initiatives.
- Native integration with the Kolver K-ducer torque wrench family.
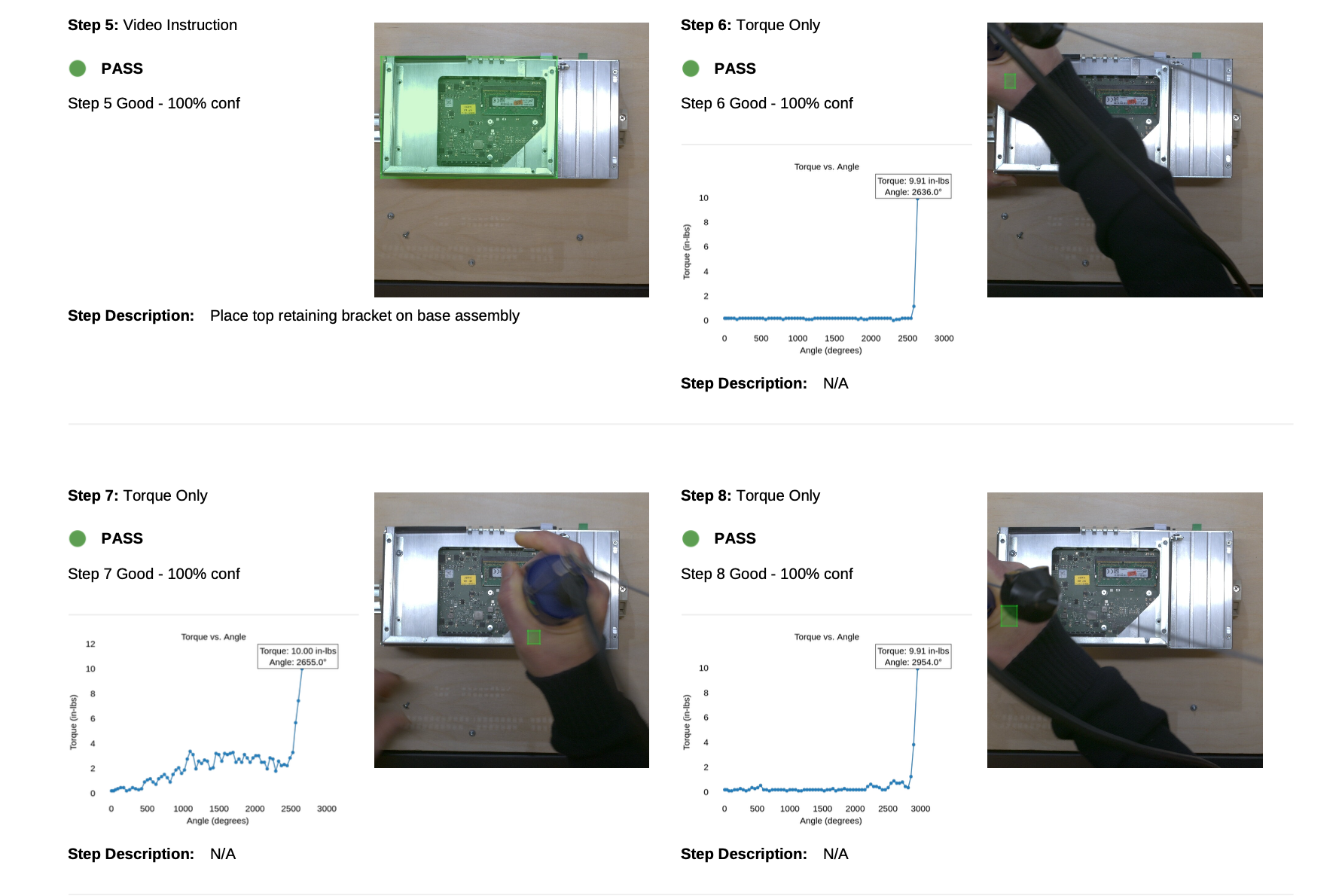
Connect with Rapta
Discover how Rapta’s manufacturing innovation can transform your fastening operations with a virtual demo.